Materize
>
Case studies
>
Prototyping facility in cleanrooms
Cleanroom based platform for development and testing of new ideas in micro and nano technologies
The Prototyping Laboratory is a facility in the cleanroom area of 680 m². Process and measurement tools provide a broad platform for the development and testing of new ideas in micro and nano technologies, based on CMOS-line technologies. ISO class 7-8.
Lithography
- Direct laser writer
- Micro pattern generator for direct writing applications and low-volume mask making
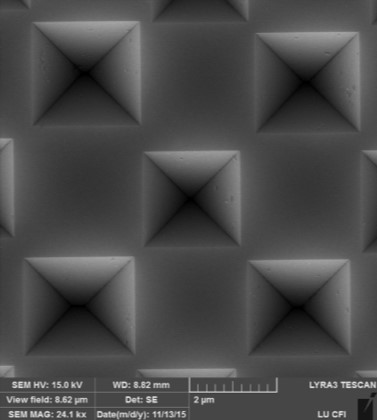
- Mask aligner
- Electron beam lithography for manufacturing structures with resolution <10 nm
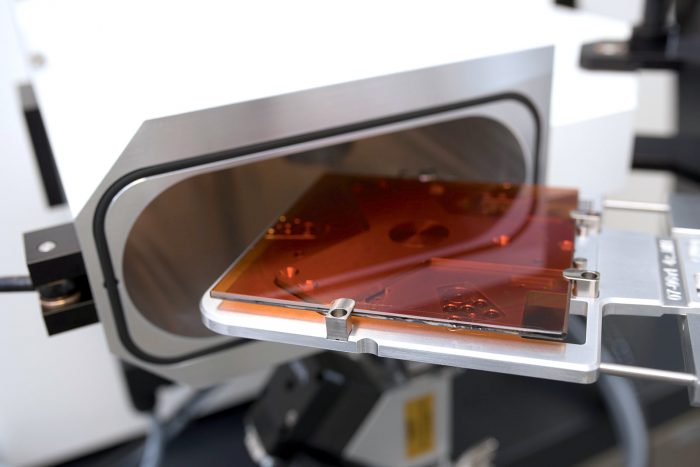
Thin film deposition
Spin-coater Laurell (2 installed)
Thermal evaporation Edwars auto 306
- Two sources for metal
- Two sources for organic materials
- Substrate size up to 150 mm
Sputter cluster SAF25/50
Magnetron sputtering cluster tool for process research and thin-film deposition
- Five chambers
- Low temperature resistive thermal evaporation
- High temp. resistive thermal evaporation
- Two magnetron sputtering – DC, RF
- Glow box loading/unloading (Ar)
Atomic layer deposition
- Deposition of ZnO, HfO2, Al2O3, AlN, TiO2, other materials on request
Plasma enhanced chemical vapor deposition (available 2020 Q1)
- Deposition of Si3N4, SiOX, PBSG (doped silica used as sacrificial layer), a-Si (p-type, n-type)
Characterization
Thickness measurements
- Dektak 150 profilometer
- Zygo NewView 7100 on-contact 3D Optical profiler
- Ellipsometer
Determines thin-film thickness and optical constants. Also composition, crystallinity, roughness, doping concentration, and other material properties associated with a change in optical response can be detected.
Electron microscopy
- Scanning electron microscope Tescan Lyra
- Transmission electron microscope Tecnai GF20
Dry etching
- Reactive ion etching (Etching technology used in micro and nano fabrication): Uses chemically reactive plasma to remove material deposited on substrates.
- Deep reactive ion etching (Bosch process): Highly anisotropic etch process used to create deep penetration, steep-sided holes, and trenches in wafers/substrates, typically with high aspect ratios.
Bonding and packaging
Wire bonder
Making interconnections (ATJ) between an integrated circuit (IC) or another semiconductor device and its packaging during its semiconductor device fabrication.
Probe station
Physically acquires signals from the internal nodes of a semiconductor device.
Dicing saw
High-speed spindle fitted with an extremely thin diamond blade to dice, cut, or groove semiconductor wafers, silicon, glass, ceramic, crystal, and many other types of material.
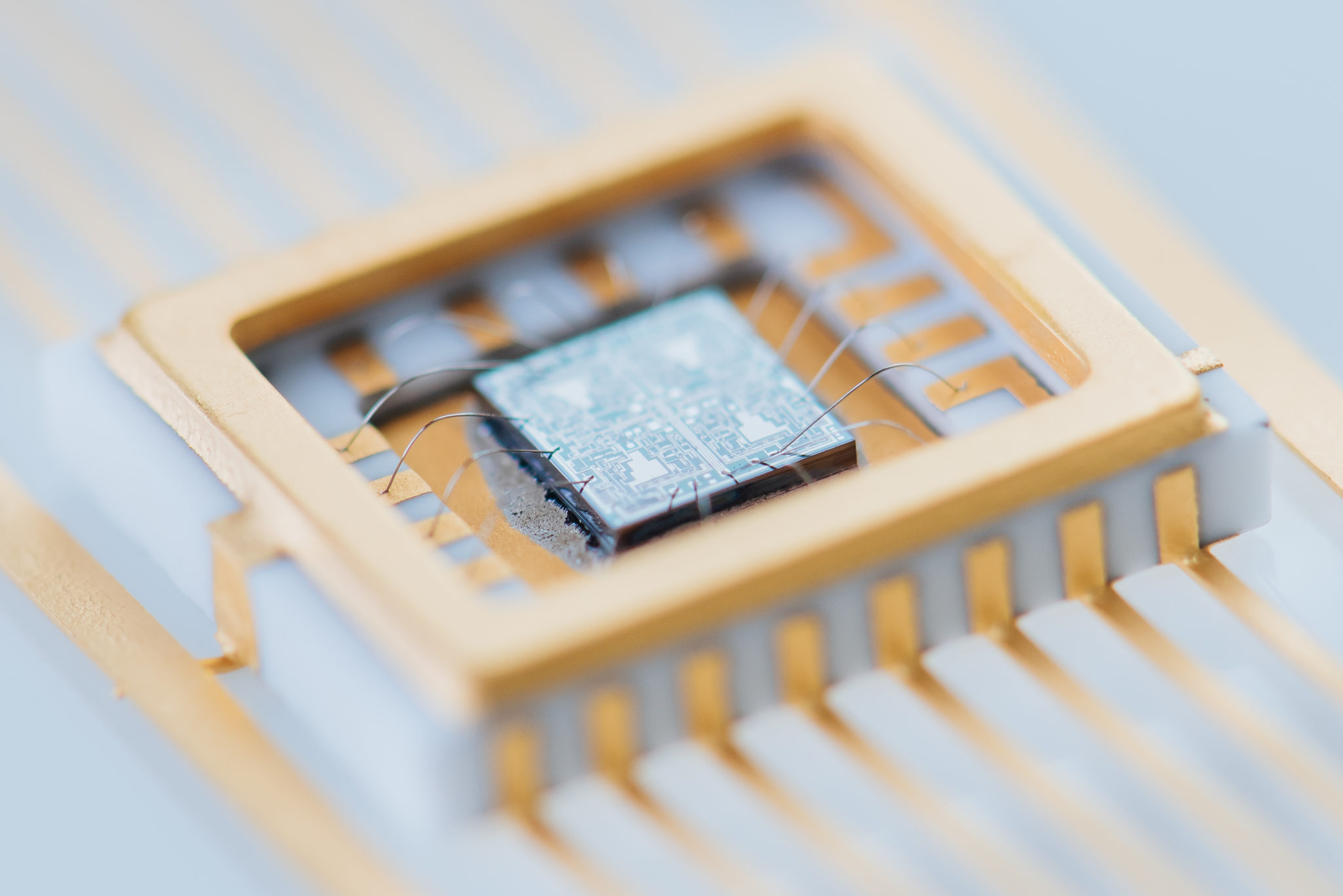
Cleaning and surface preparation
- Plasma cleaner. Surface treatment with low-pressure plasma – surface activation, surface cleaning, resist strip.
- HMDS prime oven. Hexamethyldisilazane deposition for adhesion improvement.
- UV/ozone cleaner. Surface cleaning and activation.
- Ultrasound bath. Substrate cleaning.